大径鋳抜きピンの離型抵抗による
押出しピン折損をなくす
お困りごと
D社殿では、ある金型の鋳抜きピンが大径のため、離型抵抗が大きく、離型ごとに押出しピンへ
高負荷がかかることで、押出しピンの折損が頻繁に起き、困っている。
この度、金型の更新で、成形品の押出し前に油圧シリンダによって鋳抜きピンを引抜くことにより
押出しピンへの離型抵抗を減らす構造を構想しているが、突合せ部分で成形品にバリが出ぬよう、
鋳造圧に負けない大型のシリンダが必要になる。
ただし、250tonサイズの小型ダイカストマシンを用いるため、型厚に制限があり、大型シリンダを
設置できない問題がある。
ご提案
小型シリンダでも、メカロック機構で同サイズ比170%の鋳造圧に耐えることができる
ハイパワーコアプッシュシリンダをご提案。
シリンダの小型化が可能なため、型厚を薄くすることが可能となる。
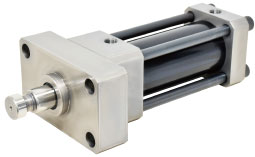
インタビュー:導入効果を聞く
ダイカストの離型抵抗問題とは?
ダイカスト成形では、離型抵抗に苦労するとお聞きしました。
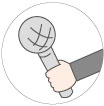
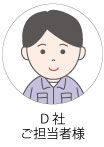
そうですね。特に鋳抜きピンがある場合は抵抗が大きくなり、
離型時に押出しピンへ負荷が掛かることで折れてしまうほどです。
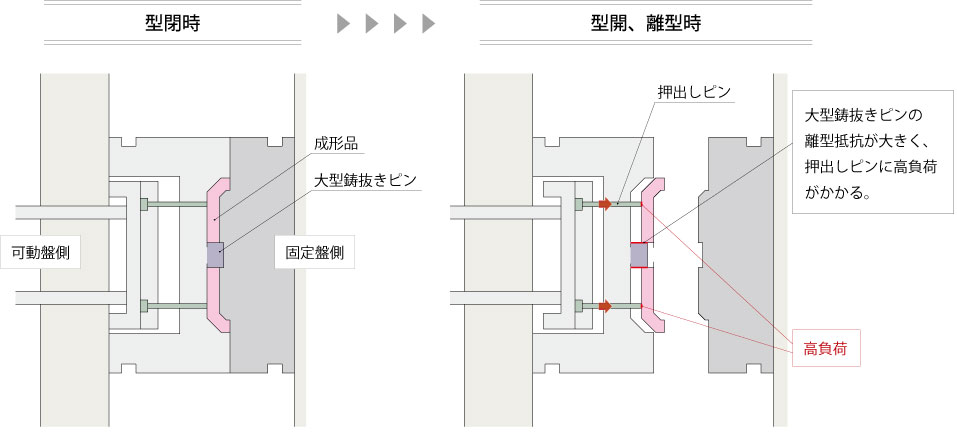
鋳抜きピンを先に引抜く油圧シリンダの採用で解決できる…?
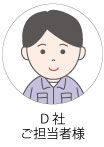
そこで、弊社では、油圧シリンダを使って
鋳抜きピンを先に引抜く構造へ改良することにしました。
なるほど、先に引抜くことで、
押出しピンへの負荷を減らすのですね。
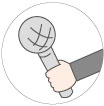
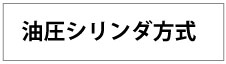
-
油圧シリンダは、前進しており、
鋳抜きピンにより成形品の鋳抜き
が可能 -
油圧シリンダは、後退し、
成形品から鋳抜きピンを離型 -
押出し時、鋳抜きピンの離型抵抗を
受けないため、押出しピンに大きな
負荷がかからずに、押出しが可能
小さなシリンダだとバリが出て…、
大きなシリンダは入らない…
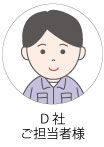
ただ、一つ大きな問題がありました。
それは、何でしょうか?
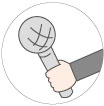
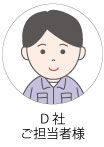
鋳抜きピンが突合せになっているため、少しでもシリンダが
鋳造圧に負けると、製品にバリが出てしまいます。
それでは、力の強い大きなシリンダが必要ですね。
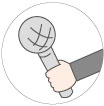
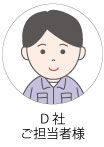
しかし、250tonサイズの小型マシンを使用するため、型厚に
制限があり、大型のシリンダを設置できませんでした…。
-
【問題点】
小型のシリンダだと、金型内に設置
できるが、力が弱く、鋳造圧に負け、
突合せ部からバリが発生してしまう。 -
【問題点】
大型のシリンダだと、鋳造圧に
耐えることができるが、サイズが
大きく、金型内に設置できない。
コンパクトかつ、大きな鋳造圧に耐えられる
シリンダがあるらしい…?
そこで、ハイパワーコアプッシュシリンダの
採用にいたったのですね。
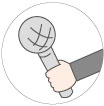
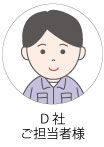
はい、ハイパワーコアプッシュシリンダは、小型の
シリンダでも、鋳造圧に耐えることができました。
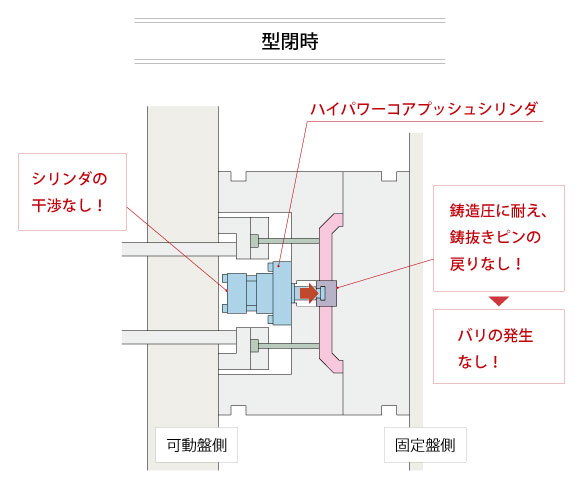
170%の力を発揮。鋳造圧にも負けず、突合せ部にもバリの発生なし。
-
ハイパワーコアプッシュシリンダは、
後退し、成形品から鋳抜きピンを離型 -
押出し時、鋳抜きピンの離型抵抗を
受けないため、押出しピンに大きな
負荷がかからずに、押出しが可能
効果の確認
・鋳抜きピンを油圧シリンダで引抜く構造としたことで、離型抵抗による押出しピンの折損を
防止することができた。
・引抜きシリンダにハイパワーコアプッシュシリンダを採用することで、型厚制限のあるなかで、
金型内にシリンダを収めることができた。かつ、鋳造圧に耐えることができ、突合せ部からの
バリの発生を防止することができた。
D社殿 導入設備
【使用ダイカストマシン】
マシン能力:250ton
【対象ワーク】
基板カバー
【導入シリンダ】
形式:PCE0630-010 (シリンダ内径φ63mm、ストローク10mm)
引抜推力:78.6kN (押側端~5mm、油圧15MPa時)